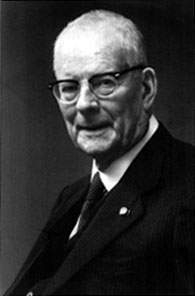
Biografía
Nació
el 14 de octubre de 1900 en Wyoming, Estados Unidos. Estudio física y
matemática en la Universidad de Wyoming. En Yale recibió su P.H. (Doctorado) en
física. Trabajó en la planta Hawthorne de la Western Electric de Chicago en la
cual 46,000 personas fabricaban teléfonos en un ambiente de explotación y mala
remuneración.
Algunas
de sus ideas de la administración surgieron de su experiencia en Hawthorne, donde
los trabajadores eran remunerados de acuerdo a lo que producían.
En 1950 la Unión Japonesa
de Científicos e Ingenieros (JUSE) invitó a Deming a Tokio a impartir charlas
sobre control estadístico de procesos. Entre junioy agosto de 1950 Deming forma
a cientos de ingenieros, directivos y estudiantes en el control estadístico de
los procesos (SPC) y los conceptos de calidad. Sus conferencias fueron
copiadas, editadas e impresas en japonés.
Los japoneses pretendieron
pagarle los derechos de autor, sin embargo Deming rechazó
la oferta proponiéndoles emplear el dinero en crear un premio para las empresas
que demostraran un comportamiento ejemplar en la mejora de calidad. Las
compañías japonesas añadieron fondos y hoy "El Premio Deming" se considera como el número uno entre
los premios de calidad. Por dicha causa los japoneses llaman a Deming "El
padre de la tercera revolución industrial".
Falleció
en diciembre de 1993, a sus 93 años de edad.
¿Qué
es calidad para Deming?
“Un producto o un servicio
tienen calidad si sirven de ayuda a alguien y disfrutan de un mercado bueno y
sostenido”.
La herramienta mediante la
cual las organizaciones comerciales e industriales pueden ajustar su desempeño
a las nuevas políticas comerciales y a la vez cumplir mejor con su misión.
El
ciclo PHVA
El ciclo PHVA, es de gran
utilidad para estructurar y ejecutar planes de mejora de calidad a cualquier
nivel ejecutivo u operativo.
El ciclo conocido como:
·
El ciclo Deming.
·
El ciclo de calidad.
·
Espiral de mejora continua.
El ciclo PHVA por justicia
se debería llamar "ciclo Shewhart", por ser este quien lo inventó,
aunque en 1980 los japoneses le cambiaron el nombre a CICLO DE DEMING:
-
Planificar:
Establecer los objetivos y procesos necesarios para obtener los resultados, de
conformidad con los requisitos del cliente y las políticas de la organización.
-
Hacer:
Implementar procesos para alcanzar los objetivos.
-
Verificar:
Realizar seguimiento y medir los procesos y los productos en relación con las
políticas, los objetivos y los requisitos, reportando los resultados
alcanzados.
-
Actuar:
Realizar acciones para promover la mejora del desempeño de los procesos.
Bases de la filosofía de Deming
·
Descubrir mejoras: Productos / Servicios.
·
Reducir incertidumbre y variabilidad en los
procesos.
·
Para poder evitar variaciones propone un
CICLO.
·
A mayor CALIDAD mayor PRODUCTIVIDAD.
·
La administración es la responsable de la
mejora de la CALIDAD.
Su filosofía
La filosofía Deming se basa
en los catorce principios gerenciales, que constituyen el pilar para el
desarrollo de la calidad. Que fueron también la aportación más importante del
doctor E. Deming para transformar la gestión en la organización y asegurar un éxito
por medio de la calidad.
PRINCIPIOS DE LA
CALIDAD
1.
Crear
constancia en el propósito de mejorar el producto y servicio.
De esta manera el doctor Deming nos
explica que el éxito para permanecer en un mercado y satisfacer las necesidades
de los clientes es mantener la perseverancia
sobre los objetivos que se persiguen para mejorar productos y servicios.
2.
Adoptar
una nueva filosofía (la cultura de calidad)
Para lograr la constancia en el propósito de mejorar
continuamente, debe aceptarse como una filosofía propia la cultura de calidad,
y adoptarla a todas las operaciones de la empresa, de esta manera la planificación
a largo plazo y el trabajo a futuro serán más fructíferos.
3.
Dejar
de depender de la inspección de todos los productos como una forma de asegurar
la calidad, ya que esto no lo garantiza.
Con un adecuado control del proceso
de producción se logra dejar de depender de la inspección para una adecuada
calidad y utilizar esta como una medida para mejorar los procesos de producción
y no para desechar productos defectuosos.
4.
Acabar
con la práctica de hacer negocio solo con base en el precio.
El obtener materia a bajo costo no asegura una reducción
de costos al finalizar el productos, ya que en el proceso pueden ocurrir
mayores inconvenientes y al final resulta más alto el precio debido a la baja calidad
de la materia inicial.
5.
Mejorar
continuamente el sistema de producción y servicio.
Con esto se busca reducir de manera
notable el desperdicio que pueda surgir en el proceso de producción, la
lentitud de los procesos y la mala atención al cliente, lo que conducirá a un
aumento de productividad y por lo tanto ser más competitivos.
6.
Implantar
la formación (instituir la capacitación en el trabajo)
Los principios anteriores deben
basarse en un programa de capacitación y buscar el crecimiento del talento
humano, para que se propicien nuevas ideas y perspectivas que son necesarias
para la mejora y la innovación.
7.
Adoptar
el nuevo estilo de liderazgo.
Los líderes establecen la unidad de propósito y la
orientación de la organización. Ellos deberían crear y mantener un adecuado
ambiente interno, en el cual el personal pueda llegar a implicarse totalmente
en el logro de los objetivos de la organización
8.
Desechar
el miedo al cambio.
Es necesario que cada miembro de la organización
este comprometido a cambiar constantemente para buscar mejorar, sin temor a opinar o participar en
las actividades que se realizan para innovar y mejorar procesos, la seguridad
es un aspecto indispensable para una mejora la calidad de los productos.
9.
Eliminar
las barreras organizacionales que impiden trabajar en equipo para lograr la
mejora continua.
Es necesario mantener un ambiente
laboral agradable para evitar rivalidades, resentimientos y falta de comunicación
entre distintas áreas, que perjudiquen el proceso de producción y el trabajo en
equipo.
10.
Eliminar
lemas, exhortos y metas para la mano de obra.
Anuncios en periódicos, carteles por toda la empresa,
murales con las huellas del personal, contribuyen al ambiente de calidad, pero
no mejoran la calidad. Estas cosas nunca le ayudaron a nadie a desempeñar bien
su trabajo.
11.
Eliminar las cuotas numéricas para la mano de
obra y fundamentar el accionar de la dirección con base en planes y proyectos,
y no en metas numéricas.
Las cuotas solamente tienen en cuenta los números, no
la calidad ni los métodos. Generalmente son una garantía de ineficiencia y alto
costo. La persona, por conservar el empleo, cumple la cuota a cualquier costo,
sin tener en cuenta el perjuicio para su empresa.
12.
Eliminar las barreras que privan a la gente de
su derecho a estar orgullosa de su trabajo.
El trabajador necesita sentirse útil
y orgulloso de su trabajo esto le permite estar plenamente feliz de lo que
realiza y esto a su vez facilita un mayor desempeño en la producción.
13.
Estimular la educación y la auto mejora de
todo el mundo.
La educación garantiza una mejora
continua en el personal, que a su vez al ser personas más competitivas realizan
un mejor trabajo que beneficia a los procesos de producción y a la organización
en general.
14.
Generar un plan de acción para lograr la transformación.
La transformación no llega sola, la alta dirección
debe tomar la decisión de querer hacerlo y aplicar el principio de instituir el
liderazgo. Para lograr la transformación debe suceder algo más que llamar al
consultor, y nombrar al "representante de la gerencia", significa
comprometerse y ser ejemplo, capacitándose primero, y cumpliendo su tarea
después.
Además de
los 14 principios, Deming nos enunció lo que él denominó “Las siete enfermedades mortales de la gerencia”
es decir, una serie de vicios que tiene el modelo tradicional de gerencia que
limita el crecimiento de la empresa.
LAS SIETE
ENFERMEDADES MORTALES DE LA GERENCIA
1. Falta de compromiso con la calidad y el
mejoramiento continúo.
Una
compañía que carece de constancia en la búsqueda de su propósito no cuenta con
planes a largo plazo para permanecer en el negocio.
2. Énfasis en las utilidades de corto plazo.
El estar revisando
cifras de cada mes difícilmente ayudara lograr la transformación en los
procesos ya que no se logra enfocar en un plan a largo plazo para poder
mejorar.
3. Estimular el desempeño del personal mediante su evaluación.
Los
efectos de estas prácticas pueden llegar a ser muy perjudiciales si se usan
inadecuadamente o de forma excesiva fomentando la rivalidad y destruyendo el
trabajo en equipo.
4. Inestabilidad y rotación de la alta administración.
Los gerentes que cambian de
un puesto a otro nunca acabarán de entender la compañía que dirigen en
profundidad, por lo tanto no serán capaces de introducir cambios a largo plazo
necesarios para una adecuada transformación.
5. Administrar el negocio solamente con base en
indicadores visibles.
No se contabiliza la
fidelidad de los clientes, la alta calidad del producto, la participación del mercado,
el conocimiento de los empleados, la capacidad gerencial, lo que se conoce como
activos intangibles.
6. Incremento en los costos de seguridad social y
ausentismo.
Con el fin de evitar que el
personal se ausente con la escusa de ir a pasar consulta y salir de las
instalaciones se cambio el concepto a medico de empresa.
7. Costos excesivos pro reclamaciones en garantía.
Constituyen
el precio directo de la no calidad. Los clientes insatisfechos deben ser atendidos
a sus reclamos y en muchos de ellos hacer honor a la garantía ofrecida ante la
imposibilidad de conseguir un producto o servicio que se ajuste a los
requisitos marcados por el cliente mismo.
Por último debemos tener en cuenta que toda actividad
es un proceso y puede ser mejorado, pero para ello todos los niveles de la
organización deben pertenecer a un mismo equipo.
Excelente aportación. Felicidades.
ResponderEliminarInformacióm muy útil, gracias.
ResponderEliminar